

Note that, during the simulation, a small queue of parts (raw material) eventually occurs. Thus, once a certain stage of the process performs far below ideal, actions can be taken to verify and correct whatever is necessary. Such reasoning (ideal x real comparison) can also be taken at each stage of the process, in such a way that it is possible to score the performance of each stage individually.
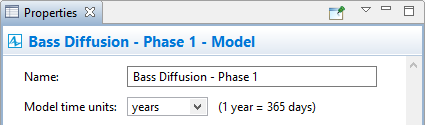
That is, it represents the maximum performance limit to which the process must be optimized. Although excessively idealized, it allows establishing benchmarks when compared to a real process. This process was modeled to represent a perfectly balanced process, which would be the goal of every production manager. They indicate the movement of items at the entrance, inside the block and at its exit. Observe the variation of the numbers next to each block. Start the simulation by clicking on the Run button. It is possible to start, pause, interrupt and adjust the speed of the simulation. Start the simulation by clicking on the Run Simulation button on the toolbar (or press F5) The modeling of this simplified process is done. The sink block is used to indicate the end of the process Set the Delay Time property to 1 minute ĭrag a sink block next to the delay block. The delay block will model the machine responsible for processing the raw material into a final product. Set the Capacity property to 50 ĭrag a delay block next to the queue block. Note that they are automatically connected. Set the source block's Arrival Rate property to 1 item per minute ĭrag a queue block next to the source tile. Start by dragging a source block to the desktop We use the blocks available in the Process Modeling Library palette to model this process. Assign a name, such as: des01 Ĭhange the time unit from seconds to minutes. There are no transportation restrictions, either from raw material to the machine, or from finished products after the machine's production ĭimensions and weights of both the raw material and the finished product are not being considered Ĭreate a new model in Anylogic.

There are no variations in the raw material supply capacity The quality of the raw material and the finished product after being processed by the machine are always considered ideal. The energy supplied by the electrical network remains stable and capable of meeting the machine's operation The machine does not require repairs or adjustments during the entire production. There are no variations in the machine's production performance (due to wear of tools or parts). There are no delays in loading/unloading parts on the machine Likewise, as soon as the raw material is transformed into a finished product, it's immediately transported to the stock. Once the raw material approaches the machine, it's loaded instantly for processing. Because trends can be volatile, you should usually only forecast 2 or 3 periods into the future.Process designed without operators. Trends observed over a short span of data could be part of a larger cycle and may not persist into the future. In this case, collect more data to determine whether the trend over a longer period of time is less consistent.Įven if your forecasts appear to be accurate, be cautious about forecasts that are more than 3 periods in the future. If the trend is changing, the model might not generate accurate forecasts. If the fits start to shift away from the data at the end of the series, the underlying trend may be changing. The fits should follow the data closely, especially at the end of the series. For example, a warehouse manager can model how much product to order for the next 3 months based on the previous 60 months of orders.Įxamine the end of the trend analysis plot and the forecasts to determine whether the forecasts are likely to be accurate. Use forecasts to predict a variable for a specified period of time.
